Various types of aircon pipe insulation are available for residential and industrial use, each with its own set of advantages and disadvantages depending on the application. To simplify the selection process and ensure optimal system performance in the long run, it is crucial to consider the requirements of the premises where the insulation is being installed.
This article specifically focuses on closed-cell pipe insulation, comparing flexible rubber with foam pipe insulation and exploring which option is better suited for different applications. Both rubber and foam pipe insulations have closed-cell structures that effectively manage condensation and thermal exchange on cold piping systems.
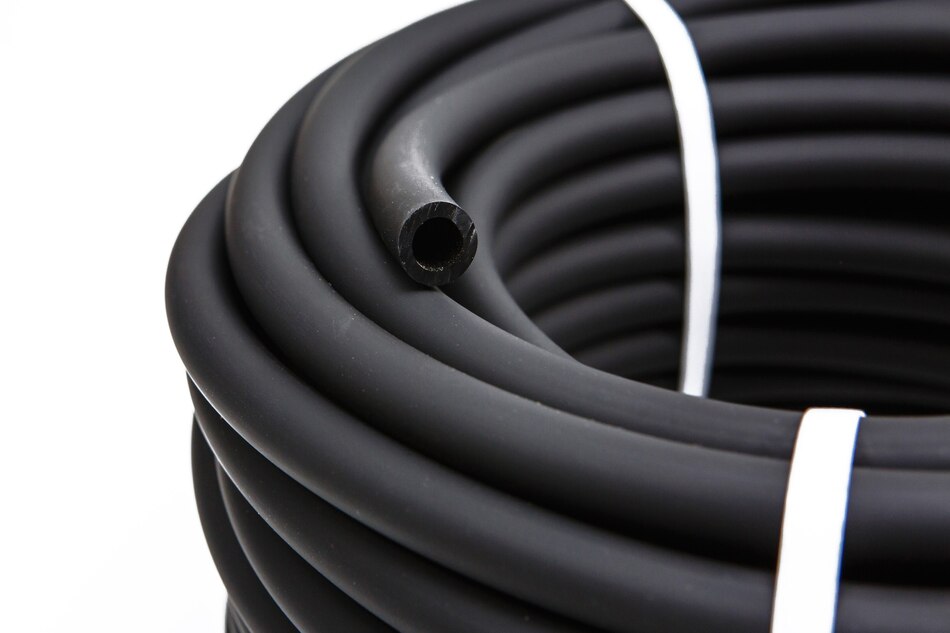
Rubber Insulation
Flexible elastomeric closed-cell foam pipe insulation, commonly known as rubber, is composed of synthetic rubber. The two primary formulations available are nitrile butadiene rubber with PVC (NBR/PVC) and EPDM (Ethylene Propylene Diene Monomer). The industry standard is ASTM C 534. A comparison between NBR/PVC and EPDM is provided in a later section.
Foam Insulation
Alternative to rubber insulation is foam insulation also known as polyethylene, polyolefin, poly, or PE. Foam plastic pipe insulation is commonly used in residential and light commercial piping systems, following the industry standard ASTM C 1427.
Rubber Vs Foam Insulation
Choosing between foam rubber and foam plastic depends on factors such as thermal efficiency, continuous service temperature, fire safety, density, and cost. Foam rubber typically offers a lower thermal conductivity (favorable K-value) than foam plastic. The upper continuous service temperature varies, with foam plastic at 200°F, NBR/PVC foam rubber at 220℉, and EPDM foam rubber at 257℉.
Fire safety is a critical consideration, with foam rubber generally passing ASTM E 84 or UL 723 tests, while foam plastic may exhibit less predictable behavior, especially at greater thicknesses.
Considering factors like density, cost, and performance characteristics, foam plastic is often less expensive than rubber.
When comparing rubber to foam plastic pipe insulation, rubber is generally preferred for commercial and industrial applications due to its lower thermal conductivity, higher continuous operating temperature, and more predictable fire behavior. Rubber is likely to meet the building owner’s project requirements more comprehensively.
You must be logged in to post a comment.